How we optimised Airshoppen's new warehouse
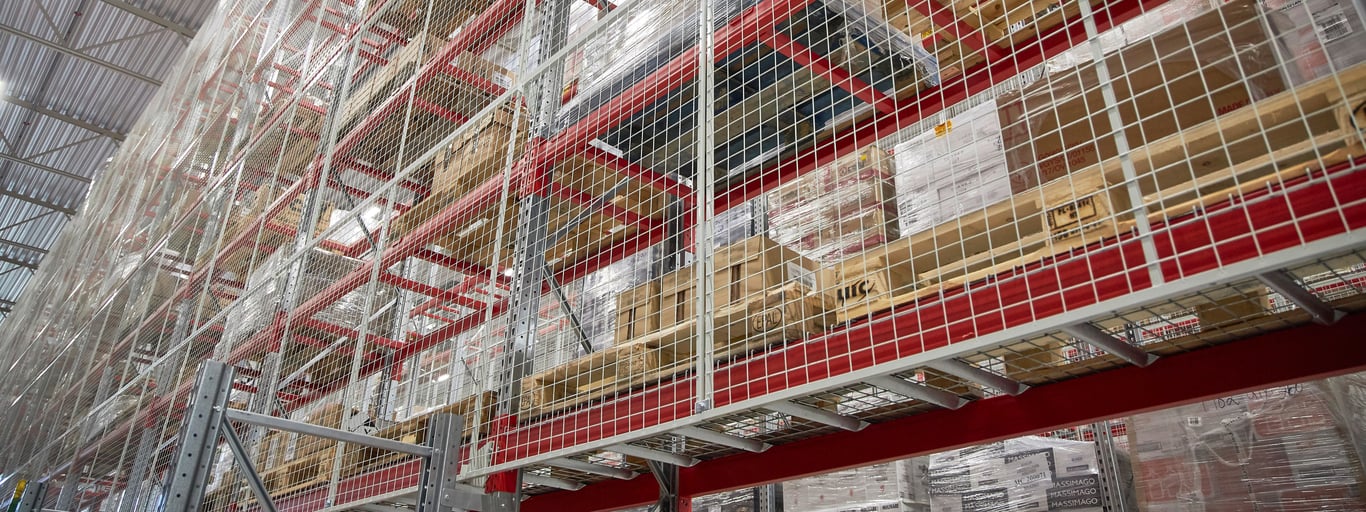
Airshoppen has been supplying duty-free goods to passengers on charter flights for more than 30 years. Before the company moved to a new warehouse in Landskrona, in south-west Sweden, it commissioned AJ Products to optimise the layout and provide fittings and furnishings for the building, which covers an area of 12,000 square metres. The result is that Airshoppen now has an efficient warehouse solution with 4300 pallet spaces and the capacity to pack 1 million parcels per year.
Airshoppen is part of the Nordic Leisure Travel Group and is responsible for packing and distributing pre-ordered duty-free goods to the group's air passengers all over the world. The company stocks around 1200 products from leading brands of skin care, perfume, jewellery, sunglasses, sweets and alcohol.
When the company decided to move its central warehouse to a new logistics facility in Landskrona in 2019, it contacted AJ Products with a specific request: to maximise the storage capacity based on the design of the building and to make sure that all the required fittings and furnishings were in position on schedule.
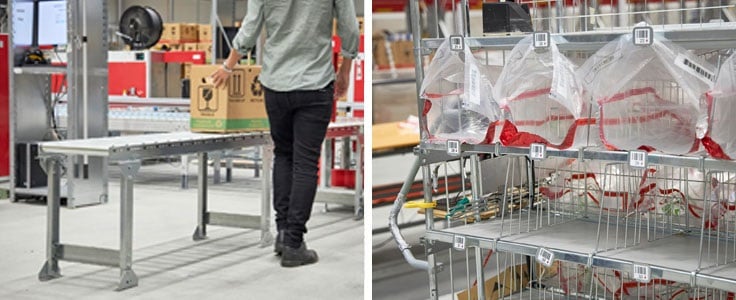
A long list of requirements
Rickard Larsson, a member of the project sales team at AJ Products who specialises in warehouse solutions, headed the project to produce a complete solution that met the customer's requirements. In addition to a space-saving layout and high-quality furnishings, the specification also included good ergonomics, efficient picking routines and a high level of safety.
"This was a task that suited us very well," says Rickard. "With our wide range of warehouse fittings and our extensive experience of large-scale logistics projects, it didn’t take us long to come up with an attractive proposal that met the customer's existing and future needs."
Once the Airshoppen management team accepted our proposal, we began focusing on all the practical issues.
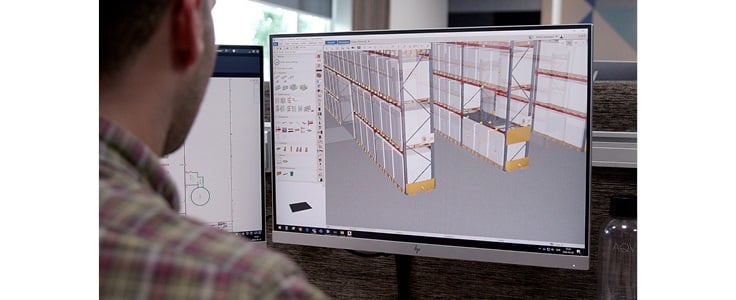
We ticked all the boxes
Armin Seceragic, a project engineer at AJ Products, was initially responsible for all the technical calculations and drawings. After that, he took on the role of the project manager right up until the customer moved into the warehouse.
"We resolved all the issues from optimising the floor plan to manufacturing, delivering and finally assembling all the pallet racking and packing tables on site," says Armin. "We had daily discussions with the customer and the building contractor. There were a lot of additional orders that we sorted out gradually, including office furniture. It was a great project!"
It is worth adding that every item both large and small was in position in the warehouse on schedule.
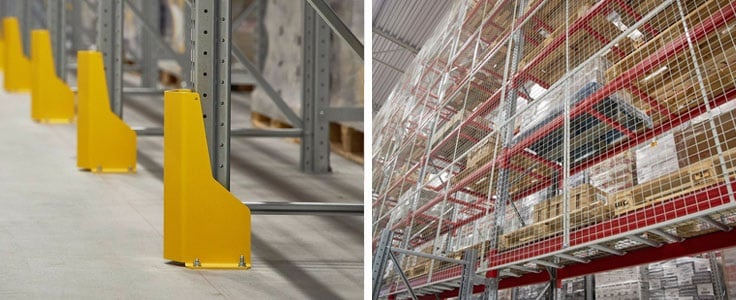
We supplied a complete solution
Our comprehensive project included everything from interior design sketches to project management and inspections. In addition, we delivered and assembled the following products:
- Pallet racking ULTIMATE with a total of 4300 individually-labelled pallet spaces.
- Around 1000 picking spaces on flow rack conveyors that are integrated into the pallet racking for the best-selling products.
- Long-side access to pallets at all picking spaces for a more ergonomic picking process.
- Safety solutions including anti-collapse panels, pallet stops, upright reinforcements, collision guards and pallet backstops.
- Additional warehouse fittings such as packing tables and picking trolleys, plus office furniture.
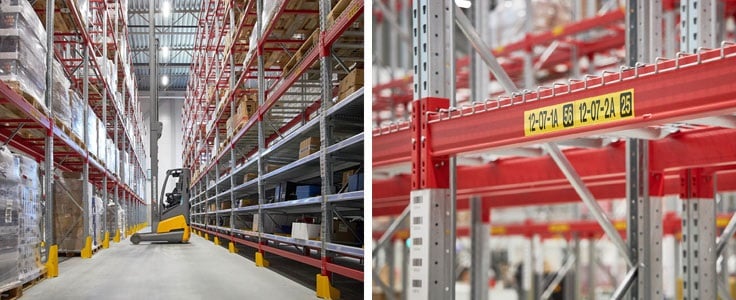
A good result for the future
Airshoppen moved into the new warehouse on schedule during the second quarter of 2020. It is now in a strong position for the future. The company has an efficient, safe warehouse with the capacity to pack around 2,500,000 products and to serve 1 million passengers per year - for many years to come!