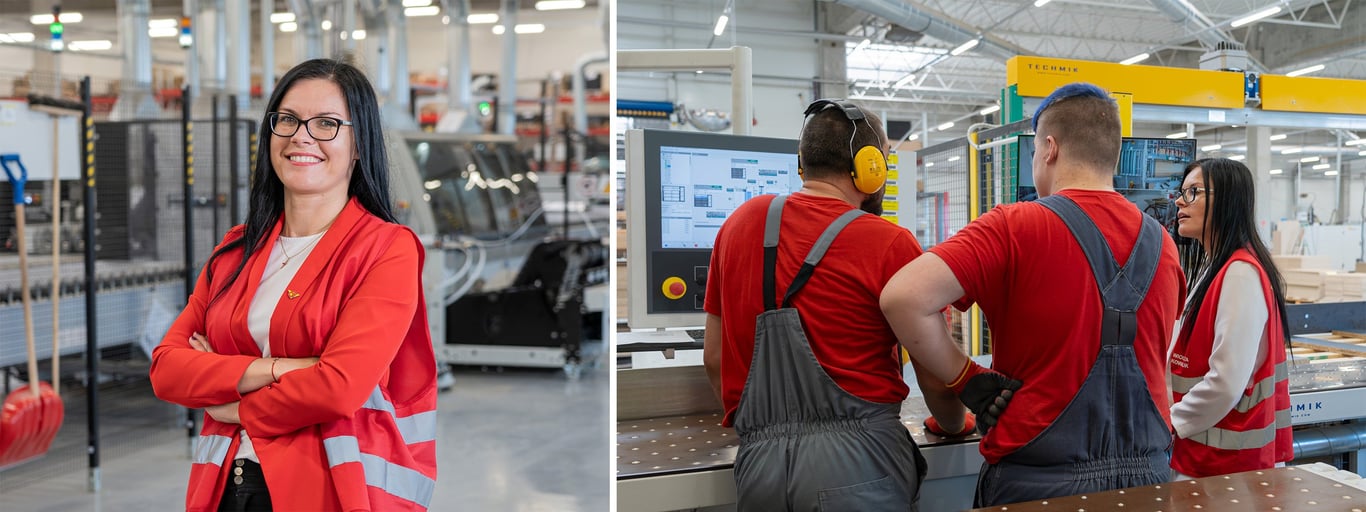
Female leadership and the kaizen method - how it became a success
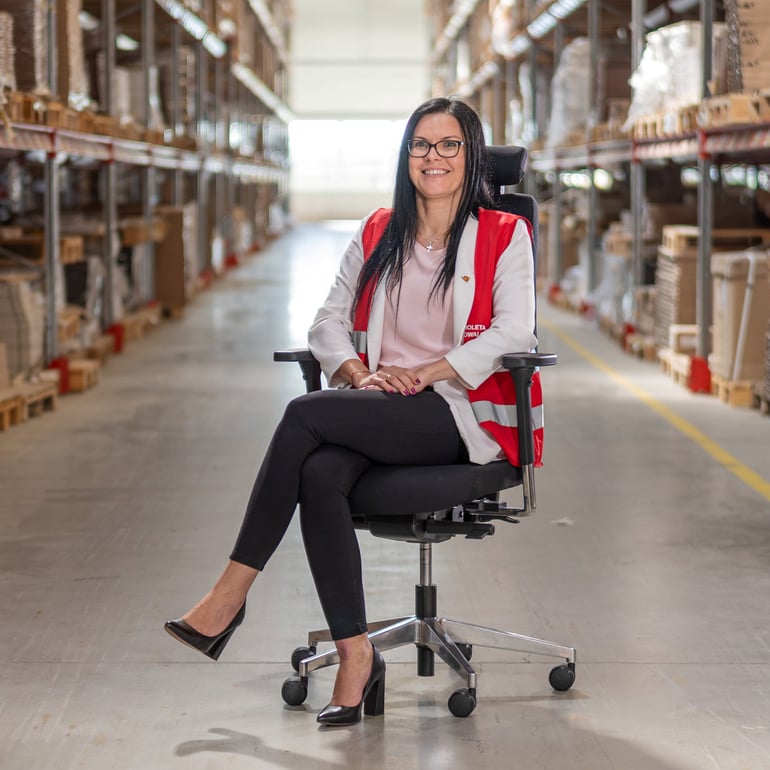
“Looking back at my career in the manufacturing industry, I realise that the hardest part has been achieving a balanced level of self-confidence and knowledge. It took me a while to understand that typically feminine traits, such as perceiving others' needs, sensitivity, patience and willingness to find a compromise, are equally necessary in business as technical knowledge.”
She believes that these characteristics help maintain a balance in the development of the company. “The biggest barriers I see lie within ourselves; overcoming them and trusting our intuition gives us a chance to follow our own path, despite the stereotypes that surround us.”
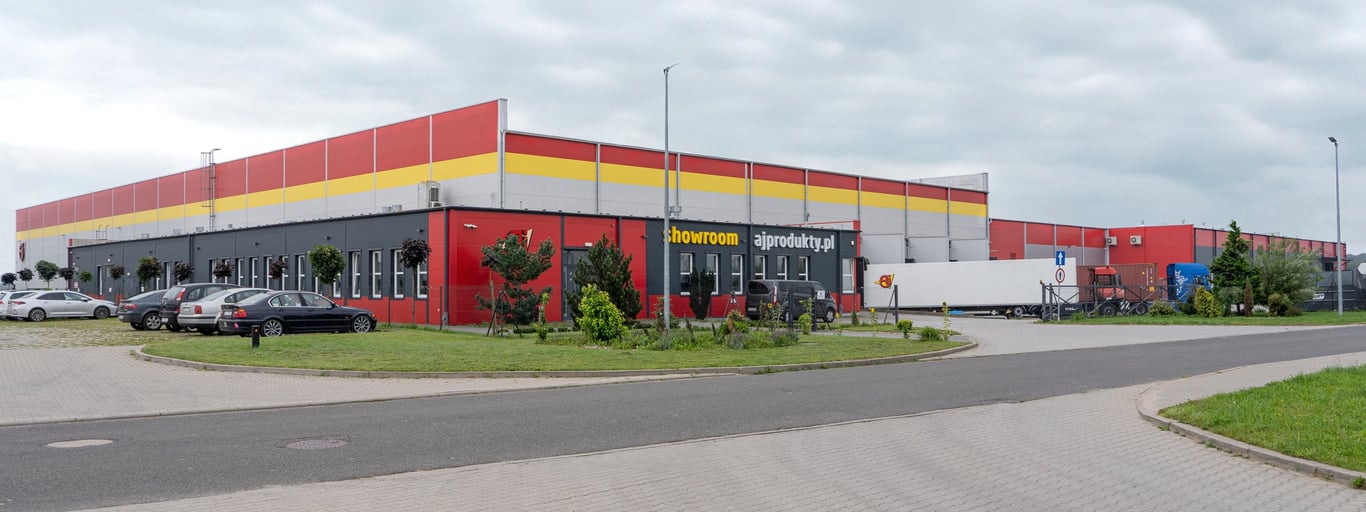
Kaizen and lean production
What was once a small carpentry shop is today a factory that sends around 25-30 trucks of furniture to AJ Products' central warehouse in Sweden every week. Led by Wioleta Kowalik, the factory is constantly being developed to optimise production and improve processes, but also to improve how the company is managed.
“Our organisation has an integrated management system based on continuous improvement. This is also one of our company's core values, so kaizen and lean are very important to us.”
Kaizen comes from the Japanese word for improvement and is a concept in business management. It is about striving for continuous development through many smaller modifications rather than through large and radical ones. This could be through improving the health and wellbeing of staff or by shortening unnecessarily long work processes. The goal is to reduce waste, for example in manufacturing. Like kaizen, lean manufacturing was also a Japanese invention. The term was coined by industrial engineer Taiichi Ohno after World War II when Japan's military industry was converted to civilian manufacturing. Lean manufacturing is a working method aimed at streamlining work methods, eliminating waste and maximising productivity. It does that by making production more “lean”, in terms of unnecessary time consumption and superfluous resources, for example.
At AJFF, kaizen and lean are a given throughout the business and are a way to always stay at the forefront and be ready to react when it comes to production. Each process is monitored on a daily, weekly, monthly and yearly basis. If the goals are not met, immediate action is taken to improve processes and there is active cooperation with each department within the organisation to eliminate deviations.

On the factory floor, IT systems are used in conjunction with physical process boards in the form of Kamishibai boards so that the department managers can get a quick overview of the current situation on the floor.
“Every day, all the managers go on a tour through all the factory departments and get an overview of the day's work. Topics such as work safety, quality, availability, technical issues and maintenance matters are then looked at and discussed. On the process boards, the factory staff can also mark if a problem has occurred in a production step, something that is reviewed during the daily tours”, says Wioleta.
Work is currently underway to digitalise the process boards so that everything will be available online and can be displayed on TV screens, hopefully before the end of the year.
Cutting-edge technology
In 2021, a system called Proxia was implemented in production, consisting of three processes, MES (Manufacturing Execution System), CMMS (Computerised Maintenance Management System), and APS (Advanced Planning System).
“During a production week, we produce a total of about 3500 orders. Thanks to the system, we can control each production order down to the second and monitor the function of the machines.”
In addition, there are Proxia computers that the staff use at each workstation where all work is continually logged throughout the day. This means that everything is recorded and can be monitored in real time so they know exactly which stage of production they are in.
“If a sudden error occurs in a machine or a problem arises at the factory, I immediately receive a message about it and we can take action right away”, says Wioleta.
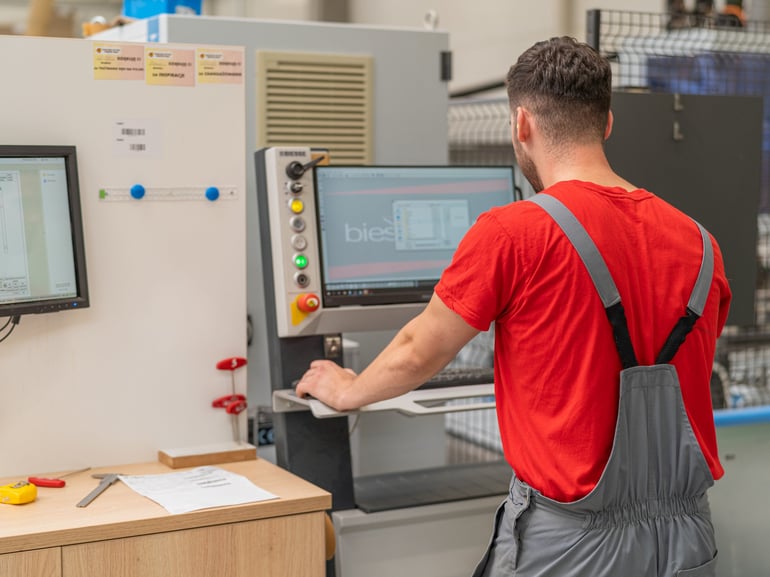
Everyone can contribute and influence
Another way the team works with efficiency and development is to allow employees to participate and influence. The staff at AJFF are encouraged to bring forward their own suggestions for improvements, whether it concerns the systems they work with or smaller things that affect their everyday life at work. Aneta Magdziarek, the HR manager at AJFF, believes that it is important for employees to feel that they have the opportunity to contribute and develop the company. Those who work on the floor see things from different perspectives and angles than supervisors do, and that is something the management team want to utilise.
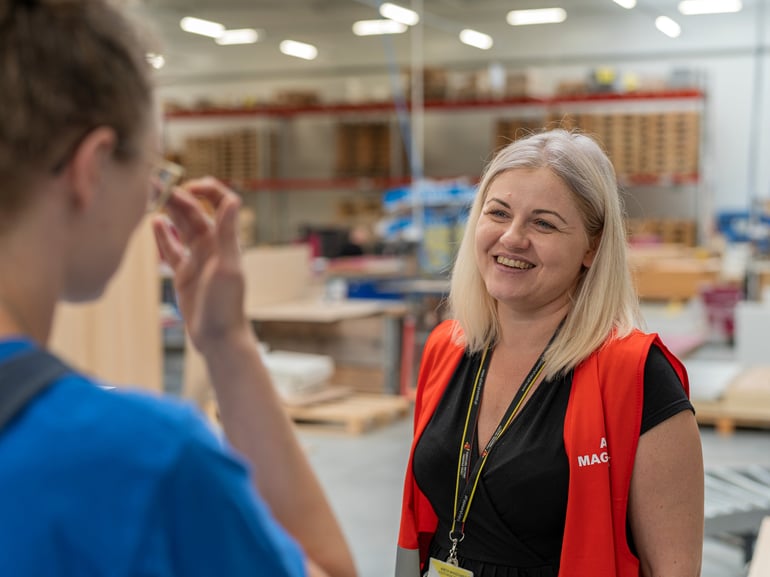
Being present as a leader
For Wioleta, it is important that the employees feel that she and others in the management team, including department heads, are present during daily work. Most of the time during her working day she is in the office but makes a point of doing a factory tour on both production floors every day, even if it’s only to check on the situation and chat a little with the employees.
“During shift changes, the department head always has a brief wrap-up meeting to go through tasks and set targets. However, it is important to also be able to have spontaneous conversations with the staff. Production is the heart of the company, but the most valuable thing we have is our employees.”
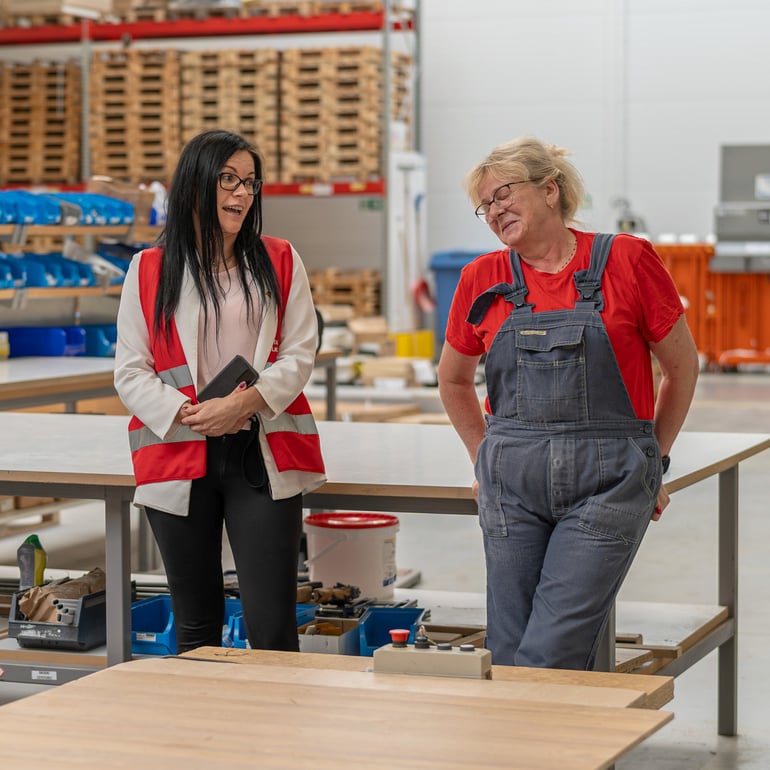
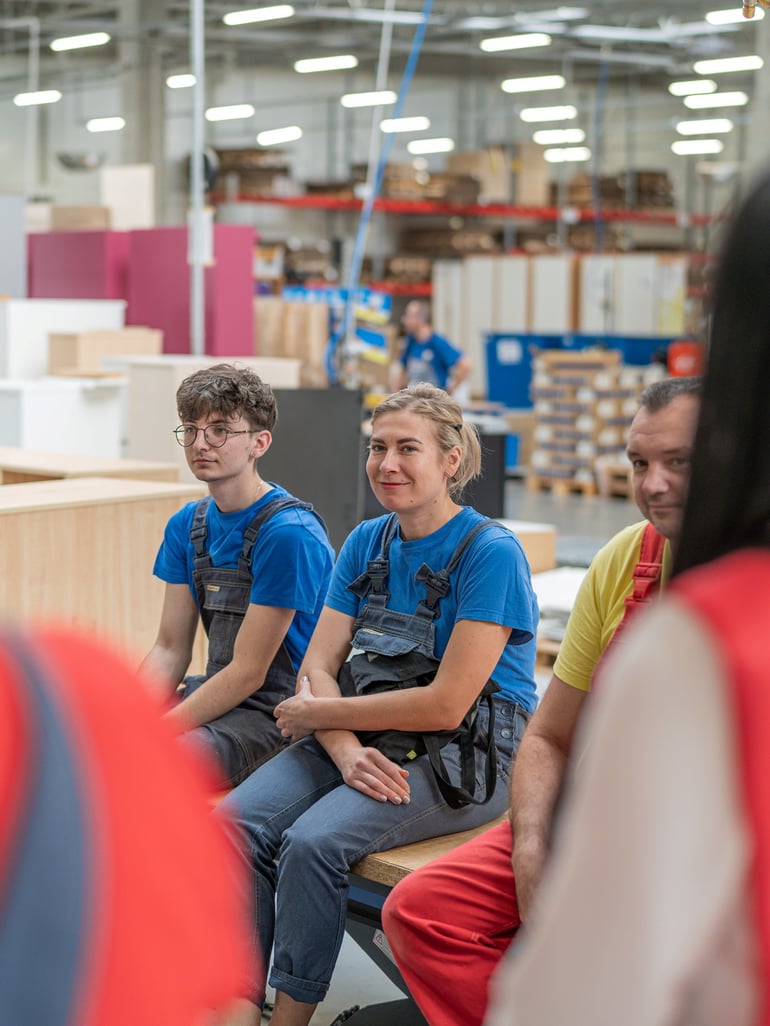
MES (Manufacturing Execution System) is a computer system for production management used by manufacturing companies.
CMMS (Computerised Maintenance Management System) is software that helps to plan, track and manage maintenance work for various types of machines, vehicles and other assets.
APS (Advanced Planning System) is a planning system that helps companies optimise their production, distribution and warehousing.